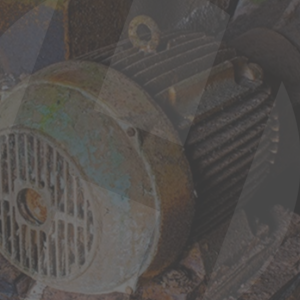
Why Motors Fail: Part 3 – The Top 5 Electrical Failures in AC Motors
July 30, 2025
While mechanical failures often dominate conversations about motor downtime, electrical issues can be just as disruptive. At HECO, we utilize a proprietary Equipment Management software known as TracRat to track our clients’ motor inventory and collect specifications, repair history, and application and performance data for each unit to enable faster asset replacement, streamline maintenance, and …